Тайити Оно (1912 — 1990) — японский инженер и предприниматель, разработал систему управления запасами и организации производства «канбан», бережливое производство (метод «Lean»), метод «Точно в срок» (just-in-time).
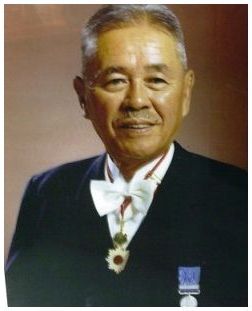
Тайити Оно родился в городе Дайрен, в Маньчжурии, 29 февраля 1912 года. В 1932 году Тайити Оно закончил машиностроительное отделение Высшей технической школы в городе Нагоя. После этого начинает работать на прядильно-ткацкой фабрике под названием Toyoda Spinning and Weaving.

В 1943 он году переводится в компанию Toyota Motor Company, где занялся совершенствованием процесса производства автомобилей. Научные разработки, как в области управления, так и технического перевооружения, всегда ценились на этом предприятии очень высоко. В 1949 году Тайити Оно становится начальником механического цеха, который впоследствии стал лабораторией развития системы поточного производства. С помощью данной системы удалось исключить из процесса производства основные виды потерь. По сути, Тайити Оно начал разрабатывать инновационные методы решения проблем, которые стали стержнем производственной системы Тойоты или Toyota Production System (TPS).
Производственная система Toyota основывается на двух базовых принципах: «точно вовремя» и «дзидока».
Принцип «точно вовремя» требует, чтобы необходимые для сборки детали поступали на производственную линию строго в тот момент, когда это нужно и строго в необходимом количестве с целью сокращения складских запасов.
Дзидока — это принцип, который предполагает автономную работу производства с использованием оборудования, способного самостоятельно диагностировать проблемы, при минимальном участии рабочего. Например: выявлять дефекты в качестве продукции или задержки в выполнении работы, сразу останавливаться и сигнализировать о необходимости оказания помощи.
В дальнейшем на основе производственной системы Тойоты, была сформулирована идея бережливого производства. Тайити Оно считал, что бережливое производство представляет собой концепцию управления производственным предприятием, в которой вся работа распределяется на процессы и операции, добавляющие или не добавляющие ценность продукту. В основе бережливого производства лежит снижение доли операций, не добавляющих ценности.
Таити Оно сформулировал 7 видов основных производственных потерь:
— перепроизводство
— ожидание
— ненужные движения
— излишняя обработка
— запасы
— перемещения материалов
— дефекты
Значительный вклад в развитие данной темы внёс соратник и помощник Тайити Оно — Сигео Синго. Если Тайити Оно знал, что нужно для устранения потерь, Сигео Синго знал, как это осуществить. Он создал метод SMED (Single-Minute Exchange of Dies — быстрая смена пресс-форм), представляющий собой способ сокращения издержек и потерь при переналадке и переоснастке оборудования.
В последствии в рамках концепции бережливого производства было выделено множество методов управления производством, а некоторые (например, кайдзен) сами претендуют на статус самостоятельной производственной концепции:
- Поток единичных изделий
- Канбан
- Всеобщий уход за оборудованием (англ. total productive maintenance, TPM)
- Система 5S
- Быстрая переналадка (SMED)
- Кайдзен
- Пока-ёкэ («защита от ошибок» и бака-ёкэ — «защита от дурака») — метод предотвращения ошибок.
За всю свою жизнь Тайити Оно написал несколько интересных книг. Одна из наиболее известных получила название «Производственная система Тойоты: уходя от массового производства». Тайити Оно в своих трудах удалось объединить мысли и идеи трех основных менеджеров XX века — Генри Форда, Сакити Тоёды и Киитиро Тоёды.

«В каждом случае мы должны докопаться до настоящей причины, пять раз задавая вопрос: «Почему?» В противном случае нельзя принять контрмеры и по-настоящему решить проблему»
«Повышать эффективность имеет смысл лишь в том случае, когда это связано с сокращением издержек. Для достижения этого нам необходимо производить лишь столько продукции, сколько возможно с привлечением минимального количества рабочей силы»
«В американской системе токарь всегда токарь, а сварщик до конца останется сварщиком. В японской системе оператор станков владеет широким набором специальностей. Он может управлять токарным станком, обслуживать сверлильный и фрезерный станки и даже выполнять сварочные работы»
«Принцип «точно вовремя» заключается в том, что во время производственного процесса необходимые для сборки детали оказываются на производственной линии строго в тот момент, когда это нужно, и в строго необходимом количестве»
(С) Тайити Оно